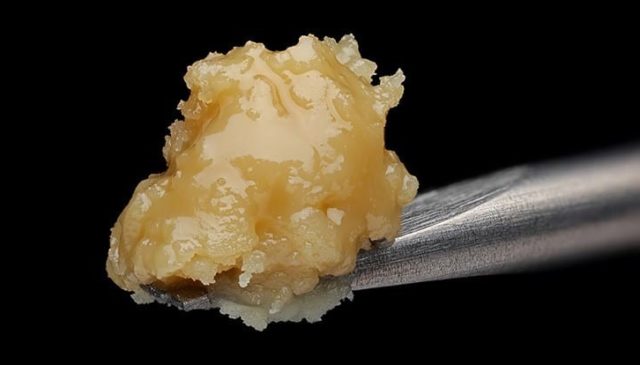
Solventless extraction can be a profitable and attractive option for cannabis processors, especially when they avoid common pitfalls.
For someone looking to launch a new extraction facility, the equipment, setup and buildout are significantly less expensive for solventless than other extraction methods, according to Ben Britton, founder and CEO of PurePressure, a solventless extraction equipment manufacturer. While solvent-based extraction equipment requires special ventilation considerations, for example, this isn’t the case with solventless, so the upfront cost of the facility buildout and equipment is generally lower.
In addition, solventless products typically sell for a premium and are popular with connoisseurs at dispensaries, Britton says.
“It also opens you up to the ability to make quality product, something that is unadulterated and hasn’t been modified by chemicals,” he says.
Here, Britton outlines his top advice for launching a profitable solventless extraction business, from acquiring high-quality raw material to establishing efficient processes.
1. Control your raw material.
Two common roadblocks for anyone processing cannabis are quality and yield, Britton says.
“At the end of the day, everybody wants the highest-quality product, and they want the most of it so that they can be profitable,” he says.
Solventless extractors use mechanical methods to separate the resin glands from the plant, and Britton says this must be a meticulous process to ensure that no particulates are lost.
Controlling the raw material is one way that processors can ensure that they have a consistent supply of high-quality cannabis that can be easily separated, Britton says.
“Time and time again, we see that the most successful businesses have really great relationships with their grow, or they’re vertically integrated, meaning that they have a grow under their umbrella,” he says. “If you can properly grow cannabis, that means that you’re properly growing good trichome heads, and that’s ultimately what we’re harvesting here. A good grow creates consistent, large, nice, bulbous trichome heads that we can then separate from the plant and collect for processing.”
For those who aren’t cultivating, creating relationships with grow wholesalers to provide great cannabis for solventless is crucial, Britton adds.
2. Start with high-quality material.
While low yield is often a common complaint with solventless extraction, Britton says this can be avoided by using high-quality material with high oil content.
“We want to make sure that we have high-quality material to start with,” he says. “You can’t extract oil that isn’t there to begin with. The maximum yield is only whatever is on that plant when you start the process.”
Yields are typically measured relative to the weight of the raw material, but if a processor knows the oil or resin content, then yields should ideally be measured against those metrics to ensure that most, if not all, of that oil is extracted, Britton says.
“That’s kind of a good way to think about things: let’s see what’s available to extract and start with something that’s as potent as possible.”
3. Handle the raw material and equipment properly.
Solventless extraction often involves fresh frozen material—a live cannabis plant that is frozen within 30 minutes of cutting and stored in a vacuum-sealed container to ensure that it has the highest terpene retention. If fresh frozen resin glands are exposed to higher-than-ideal temperatures, which exceed 40 degrees Fahrenheit, they can easily transfer, melt or be lost entirely, Britton says, so it is critical to handle and store the material properly throughout the extraction process.
If a processing facility does not have its own grow attached, vendors should maintain the fresh frozen flower at freezing temperatures during transit, and this should be maintained within the extraction lab until it is processed.
“We just see those steps being overlooked,” Britton says. “A lot of people are excited to get the new extraction equipment that they know is going to produce the oil, but maybe look over some of the finer details in between.”
When the material is ready to be processed, extractors must ensure that their equipment, such as rosin presses and hash washing gear, is in proper working order to maximize yield, he adds.
“When we’re going through the filtration process with ice water extraction, we’re typically filtering micron-sized particles anywhere in the neighborhood of 25 to 160 microns in diameter, and we’re straining that out of, say, 65 gallons of water,” Britton says. “You’ve always got the opportunity for that particulate to be lost if, let’s say, your filtration media has a hole in it, or you have a leak somewhere.”
Therefore, processors must be meticulous, ensuring that their filtration media is inspected and that all gaskets are in place before use.
“These are simple things that sound trivial, but it ends up having a pretty dramatic impact,” Britton says. “Make sure that before you start washing to make ice water hash, that your water and your vessels and all of your fittings have actually come to temperature at about 32 to 33 degrees Fahrenheit. You don’t want that material to come into contact with a warm vessel wall, or it is going to stick to that vessel.”
4. Lay out an efficient extraction process.
Extractors should have a clear and defined processing schedule for their facilities to ensure that material moves smoothly through the process, Britton says. This is especially important for processors who use solventless extraction, as they often deal with fresh frozen material that must be handled properly throughout the process to avoid damage and loss.
“Having a good extraction process laid out will help you with your efficiency and making sure that when the product finishes from one process, you’re ready for it to move on to the next process, or you at least have a way to store that material,” Britton says. “We’ve seen issues where people just kind of go in gung-ho and start producing, but they don’t have all their subsequent processes lined up or timed properly. It’s the equivalent of having the turkey on Thanksgiving come out at noon and everything else is ready at 4 in the afternoon—it’s not going to work out so well.”
Britton encourages those looking to launch or optimize their solventless extraction operations to contact PurePressure for additional information.