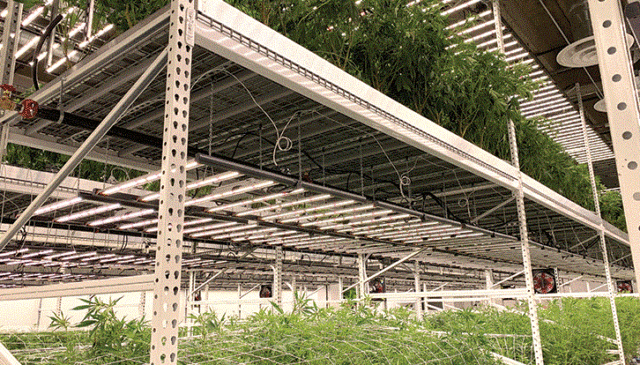
Editor’s Note: This article was originally published in the November 2020 State of the Lighting Market, produced by Cannabis Business Times and made possible with support from Fluence by OSRAM. Read the full report in the November issue of CBT.
As chief scientist for LivWell, Andrew Alfred’s priorities include testing any potential facility update or growing change before implementing it at scale.
For the past seven years, one of the inputs Alfred has researched extensively is lighting. Alfred was interested specifically in light-emitting diode (LED) technology for its energy-saving potential, but before considering a widespread change for the vertically integrated company’s 2-acre canopy in its flagship cultivation facility in Denver, he wanted to be sure plant performance wouldn’t suffer.
“Seven years ago, one of the LEDs that we had in our flower rooms looked like a car engine. It weighed 80 pounds,” Alfred says. “We didn’t know how to use the LED light. We didn’t know that you had to raise the temperatures in your room to account for the loss of radiant heat.”
Another common mistake cultivators made in the early days was simply swapping out one grow light for an LED light without calculating lighting density, which was “a growing pain that the industry had to reconcile.”
However, both LED technology and cultivator knowledge have improved dramatically and quickly, Alfred says, and that includes everything from the lights to the mounting hardware. Working with nearly 20 North American and European LED lighting manufacturers, LivWell has conducted multiple cannabis trials over the years, adjusting environmental conditions to optimize plant performance.
Because of the improvements in yield and energy savings, for the past five years, the company has been incrementally converting its entire Denver facility to LED lighting and has almost completed the transition.
Here, Alfred shares some key takeaways he’s learned and tips for cultivators who are considering a lighting retrofit in an existing facility.
1. Experiment before implementing any sweeping change.
Before updating lighting, Alfred recommends requesting samples or investing in a few lights and testing them first, comparing them to current fixtures and observing metrics like yield. Ensuring all parameters are adjusted for new lights, especially temperature, is also important when running trials “to make sure it’s a fair fight,” he says.
“The important thing to remember with temperature is that it is all about the plant, not just the temperature of the air. You can use tools like infrared thermometers to measure canopy temperature,” he says. “Given the same air temperature, a plant under LED could easily be 5 degrees [F] cooler than a plant under HID [high-intensity discharge],” which could negatively impact yield. Raising the air temperature, targeting ranges in the low 80s, can be a successful strategy for growers.
2. Create detailed plans and review them with all involved.
Replacing existing growing lights for LEDs has been a five-year-plus project for LivWell, and in a few months, the transition will be complete. Creating a plan was integral for success, Alfred says, as was reviewing those plans with the lighting manufacturer and engineers. “You have to bring a lot of people to the table to plan that transition,” he says. “We had to coordinate with all parties involved, such as the lighting manufacturers, electricians, [environmental] controls company, permitting office and our production staff.”
3. Establish a relationship with your utility company account manager and ask about rebates.
Once LivWell reviewed and finalized the plans with the lighting manufacturer and engineers, they sent the details to their utility company for rebate pre-approval. Establishing a relationship with your utility company account manager is important for many reasons, whether you are planning on updating lighting or not, Alfred says. When LivWell first explored converting to LEDs, Alfred contacted his account manager to discuss the project and if they qualified for custom rebates.
Colorado was still a young market then, and the electrical engineers from the utility company were accustomed to measuring light using lumens, not photosynthetically active radiation (PAR), Alfred explains. By establishing a partnership with the company, he was able to demonstrate the importance of PAR and the significant savings from LEDs.
Now, engineers from the utility company regularly visit LivWell to review the lighting work and measure energy usage. And for every LED light LivWell has purchased, the utility provides 25% to 40% cash back on the investment.
“It takes a big burden off their power grid,” he says. “It’s better for our business, and it’s better for the utility company.”
4. Install incrementally to minimize downtime.
Once a rebate program is established, the operations team steps in to coordinate the installation, permitting requirements and construction details.
Minimizing the time that cultivation areas are offline is the most challenging aspect of a retrofit, but LivWell was able to do this by working through careful logistics and installing new lighting incrementally. For LivWell, sometimes that meant using a flowering room as a vegetative room temporarily while the actual vegetative room was being converted.
“If all equipment is staged and permits are in order, it can easily be done in under a month. If any of those pieces are missing, it can take a lot longer,” Alfred says. “We had to be flexible with what kind of cultivation we did where to keep our production cadence going.”
Because LivWell runs a perpetual harvest, sometimes they worked row by row, converting lights as each bench was harvested, using tarp barriers as temporary walls to protect plants.
“It really is kind of a monumental effort, and when it’s done too casually, it might result in lost production,” he says. “A good general contractor can quarterback the coordination.”
5. Recalculate sensible loads, and consider other important measurements.
Because HVAC equipment is designed and set to work at specific sensible and latent loads, LivWell needed to work with engineers to recalculate the ratios based on the new lighting that does not emit as much radiant heat.
“A more technical challenge was figuring out how to keep our humidity setpoints while removing 40% of our sensible heat load,” Alfred says. “We worked with our engineers to assess our HVAC’s equipment to handle this change and, in some instances, found that we needed to upgrade our units. It’s very important that anyone considering retrofitting to LEDs do this calculation beforehand.” In some cases, it will require an equipment upgrade, or, at the very least, a setpoint change. “You don’t want to go in blind without having thought through that first,” Alfred says.
6. For vertical systems, calculate humidity, temperature, and extra floor space required.
Because LEDs emit far less radiant heat, growers who convert to this technology sometimes explore using vertical (tiered) growing systems, as lights can be closer to the plants. Although “the sky is the limit” regarding how many tiers cultivators could theoretically have, Alfred recommends caution here. LivWell sticks to two tiers in flower and stops at three in veg.
“The higher you go, the more challenging it gets,” he says. “It can be difficult to make sure temperature, humidity and air movement are equivalent across all tiers. You don’t want your top tier to be a different temperature than your bottom tier, which can happen, especially as you get taller and taller cultivation systems. You can get these stratifications of environment. It’s just like switching to LED, and if you’re switching to vertical growing and LED at the same time, there’s an extra layer of making sure that you do your homework.”
Cultivators must account for extra floor space needed for equipment in multi-level systems, as well, Alfred says.
“Consider how aisle and bench widths need to change between single-level and multi-level systems. You’re going to need wider aisles for bringing a roller ladder … and you’re typically going to want narrower benches to access the plants,” he says. “This means that going vertical doesn’t simply translate to two times or three times more canopy.”
7. Have backup plans–and lights.
With all that’s involved in a lighting conversion, unexpected problems can come up, and that includes issues with lighting equipment.
“Have a tough conversation with your lighting manufacturer about their equipment failure rates,” Alfred says. “Less than 1% is a bare minimum starting point. Then, make sure the manufacturer sends surplus inventory to anticipate the need to immediately swap out lights that have issues. If a manufacturer can’t speak to what their failure rates are, that’s a red flag that they don’t have a lot of experience with quality control and field installations at scale.”
Retrofitting an existing facility with live plants can be challenging, Alfred says, but it’s been worth it for LivWell.
“The LEDs often pay for themselves in 12 months just in energy savings alone,” he says.