Glass House Farms recently launched a new 1:1 cultivar in partnership with FRB Genetics, providing the California cannabis market with a flower product that dials in the THC and CBD ratio pretty evenly. It’s called Tangelo Flo, and it’s finding its way to the market at a time when industry stakeholders and consumers are having in-depth conversations about potency, chemical profiles and minor cannabinoids.
Tangelo Flo offers a balanced cannabinoid profile (a “type-II” chemotype, in parlance that’s making its way into the commercial space, meaning one that features a mixed-ratio cannabinoid profile). Even as high-THC cultivars and products continue to top the sales charts, industry chatter is keen on a more balanced suite of chemicals. That’s where FRB Genetics’ R&D work has taken the team, led by Reggie Gaudino.
A cross of Green Crack and Cherry Wine, the new cultivar boasts approximately 31% total cannabinoids and a rich, citrus-forward mango flavor. Green Crack is a THC heavyweight, and Cherry Wine is a popular hemp variety.
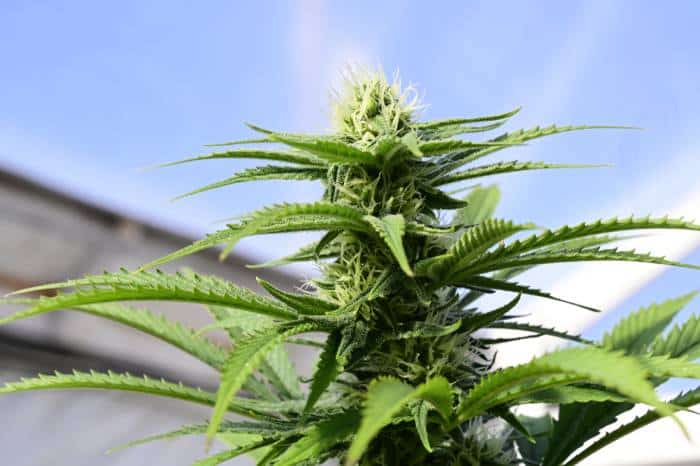
Courtesy of FRB Genetics
Front Range Biosciences runs a marker-assisted hemp breeding program, and the Cherry Wine options were fairly limitless for the FRB Genetics team. (FRB Genetics licenses the breeding technology from Front Range Biosciences, which is not a plant-touching company.) Gaudino’s wanted to showcase some of the good work being done on those hemp varieties—and perhaps usher those genetics into the broader adult-use cannabis space.
The Cherry Wine side of the equation posed an interesting challenge, because Gaudino’s team was looking for a high CBD producer that could also remain compliant as a hemp variety (clocking in under 0.3% THC content). That’s no small task. This process involved thousands of seeds and countless hours spent observing the different Cherry Wine plants. They landed on an ideal phenotype, one that brought a robust plant structure and healthy yield to the breeding process with Green Crack’s THC powerhouse lineage.
The parent plants here offered a vitality that would make growers’ jobs much easier—something that’s important when bringing commercial considerations into the breeding process.
“It finishes relatively quickly, so it’s good to work with in a commercial cannabis environment,” Gaudino says.
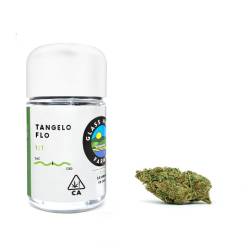
At Glass House Farms, that commercial cannabis environment spans more than 500,000 square feet of greenhouse space in southern California. Glass House Brands President and Chief Cannabis Officer Graham Farrar says that Tangelo Flo has been a manageable cultivator—relatively simple to grow, easy on the eyes. More importantly, thought, Farrar is excited to get something like this onto store shelves. He says there’s a broad swath of consumers who are looking for products with this sort of chemical profile.
“Daily, everyday cannabis—I call it the ‘missing middle,’” he says. “We either have connoisseurs—people who have been here for 20 years and they jump through all the hoops and they go to the doctor to get their medical card—or we have the people who just walked in the door and they don’t know, in tequila parlance, 1942 from Jose Cuervo, right? My belief is that the middle is going to show up.”
Lower THC, higher CBD, a more even-keeled ensemble of effects: There’s a certain convenience and simplicity in a cultivar like that. Tangelo Flo is one of the early steps forward into that variation in the cannabis marketplace.
As for what’s next from FRB Genetics? This certainly won’t be the last 1:1 cultivar the team delivers. And Gaudino hints at more to come: “Besides this 1:1, we actually have a number of other 1:1s that are in the pipeline of development, which are based on trying to track down very specific terpene profiles that are very rare in the cannabis industry,” he says.