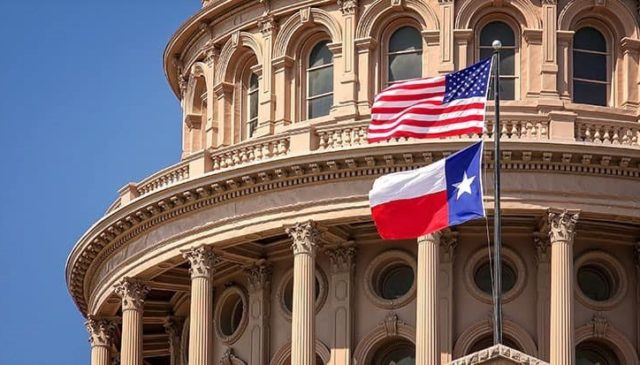
This is a story about heat and pressure.
And cannabis.
Centuries ago, the original cannabis concentrates were made using hand-pressed hashes, with communities on the Indian subcontinent using their hands to make charas. To use modern lingo, these were solventless concentrates, not all that different from products that consumers are finding on dispensary shelves today.
“The origins of solventless go all the way back to the beginning of when hash was first discovered,” Eric Vlosky, PurePressure’s director of marketing and business development, says.
In the 1980s and ‘90s, bubble hash had a moment in traditional cannabis markets before butane extraction gained a certain prominence in the 2000s and into the 2010s. In 2014, Phil “SoilGrown” Salazar used his girlfriend’s hair straightener to squeeze a cannabis bud and noticed an enticing oil spilling out. Here we have the creation of modern rosin. The solventless extraction industry has grown steadily ever since.
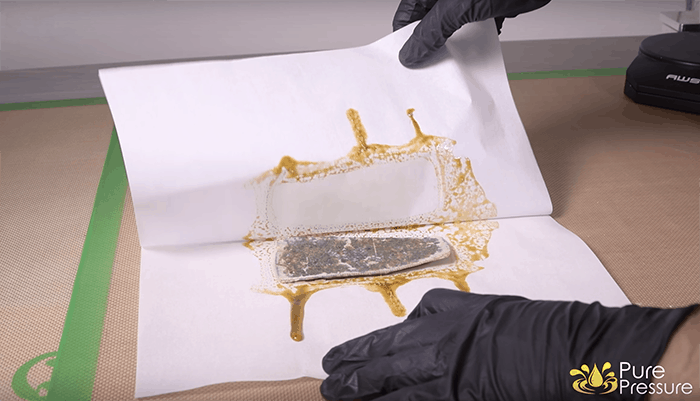
Courtesy of PurePressure
In 2015, PurePressure was formed to address this new demand. Co-founders Josh Rutherford and Ben Britton worked together to engineer a better press than what was on the market at the time (mostly repurposed T-shirt presses). The original prototype worked exceedingly well, and the company was off to the races.
So, what is solventless extraction?
The end products include live rosins, diamonds, shatter, wax, budder, sugar, sauce, oil: Much of the same categories that can be produced in a solvent-based process, but with the essence of the plant material kept in place. Live rosin, for instance, is differentiated from live resin by this very process. And, bear in mind, product innovation is happening at a rapid pace now, so this is an ever-changing landscape within the broader cannabis market.
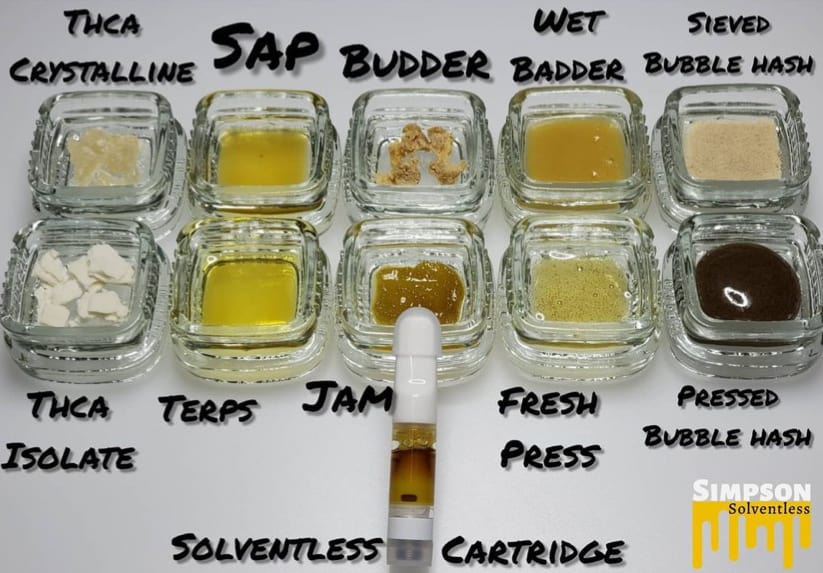
Flower rosin is another segment of this category, a more budget-friendly option for experimenting with solventless—one that may involve more organic plant matter on the front end.
More popular inputs include dry sift and ice water hash. Ideally, plant material is fresh-frozen before being used as a solventless starting point; this preserves the very nature of the cultivar that’s being directed into a concentrated product.
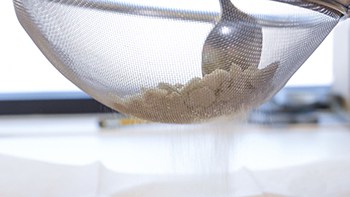
Photo courtesy of PurePressure
“The reason most great rosins are made with live product, meaning fresh frozen, which is then washed, is because it really preserves more of the volatile terpenes, the monoterpenes, the sesquiterpenes,” Vlosky says.
This—the live rosin origin story for the modern processor—is the key to the rise in solventless extraction.
The “rosin” nomenclature is important, because there’s not yet a regulatory agency that oversees these distinctions, per se. Whereas live resin comes from hydrocarbon extraction processes using fresh frozen plant material, live rosin denotes a solventless end product. “Resin” is a bit of a catch-all term, to an extent, but “rosin” clearly applies to solventless extraction methods: heat and pressure achieving the original expression of each cannabis plant’s flowers.
It’s a market segment that’s gaining traction across the U.S., primarily because solventless extraction retains the clearest presentation of the original plant material in its many final forms. The live rosin product category is honed and marketed for the cannabis connoisseur, but now many consumers who are looking for a higher quality experience are starting to gravitate to solventless products as well.
While newer cannabis markets might initially open to great fanfare within the flower segment, consumer education tends to dial in more nuanced preferences for cannabis consumption—leading many to seek out the lively terpene expressions and flavors of solventless products.
It all goes back to the careful preservation of the cannabis plant’s natural resins.
“When you’re applying heat and pressure to trichomes, which are these very small, delicate little structures, the cell wall and the trichome head and stalk ruptures,” Vlosky says. “The heat is what helps liquefy that oil to a point that, combined with pressure and a filtration medium, since it’s pressed in a bag or in a stainless steel wrap, extrudes and presses the oil through the filter, giving you the pure expression of the plant. It’s leaving a lot of the organic plant material behind, like the husks of the trichomes and any other residual plant material.”
WATCH: Click here for a video of rosin being pressed on a PurePressure press.
To get it right, rosin presses should include rectangular heat plates. A square isn’t ideal, because that shape creates less perimeter space for the rosin to “exit” the press—meaning, in the end, less yield from the plant. There are several variables in play here, but PurePressure encourages using a rectangular bag on a rectangular heat plate to ensure that the perimeter is used most efficiently.
“You want to reduce that distance [from the center of the plate] as much as you can, and there’s a bit of a balance there,” Vlosky says.
Ultimately, it’s both science and art. Finesse is a critical part of the actual pressing process.
The bottleneck, to the extent that producers watch out for one, is not with rosin presses, but rather with source material production itself. How much hash or sift can your produce? Most operators find that one or two presses gets the job done, though there are certainly businesses running six or even eight presses every day.
PurePressure has designed its equipment to more easily navigate the learning curve. The company’s rosin presses include touch-screen feedback mechanisms to convey how long you’re pressing and how much force you’re applying. The presses are loaded up with established recipes (and room to save your own for later reference). That’s another key: The savvy operator will want to track and record all measurements—input and output—to ensure that the highest-quality yields are emerging from this process. Then it’s easier to scale and figure out if it fits into your business model.
Because the solventless process retains the plant’s true expression, this isn’t a situation where plant material can be remediated. If the plant material has issues on the front end, those will be picked up on the back end.
“What goes in absolutely comes out with solventless,” Vlosky says.